February 14th, 2024
Category: ar vr,virtual reality
No Comments
Posted by: Team TA
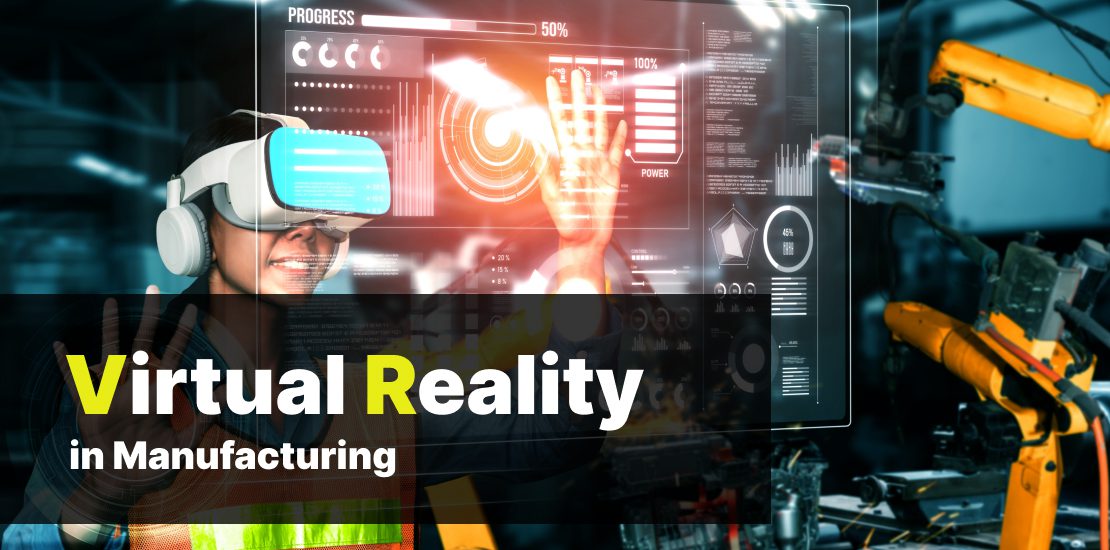
Virtual Reality in Manufacturing
Virtual reality technology has emerged as a powerful tool within the manufacturing industry, bringing radical changes to traditional processes and improving overall efficiency. The integration of VR into manufacturing operations has led to significant advancements in training, design, collaboration, and maintenance.
According to SkyQuest Technology, the market value of virtual reality (VR) for the manufacturing industry will reach USD 50.42 billion by 2030. A recent report by PwC shows that 68% of manufacturers value VR training to bridge the skills gap in their workforce. The use of virtual reality is becoming a strategic necessity for manufacturers in today’s competitive and dynamic marketplace.
A Historical Perspective of VR in Manufacturing
Throughout the history of manufacturing, there has been a constant evolution from traditional craftsmanship to modern techniques. In the past, people used to make things by hand using simple tools, which was slow and often resulted in products of varying quality. During the Industrial Revolution, people began to use technology to make things more efficient, which led to the development of assembly lines. However, this also brought new challenges like increased complexity and less flexibility in manufacturing.
Recently, Virtual Reality (VR) technology has become a game-changer for the manufacturing industry. VR allows workers to experience lifelike simulations that help them learn and acquire new skills quickly. This technology has helped to improve efficiency, safety, and precision in manufacturing processes. VR has become an essential tool for the industry because it addresses many of the challenges faced by traditional manufacturing methods.
Best 5 Applications of VR in Manufacturing
1. Design and Prototyping
VR enables engineers to collaborate and prototype designs by visualizing and modifying 3D models in real-time. This process helps to reduce the time required for product development iterations, improving productivity. Manufacturers can hence attract investments, increase innovation, and speed up the time it takes for their products to reach the market. According to a survey conducted by Deloitte, 86% of manufacturing companies that used VR in product design reported improvements in design quality.
2. Training and Skill Development
Virtual Reality (VR) training offers a cost-effective and efficient way to train employees on new equipment and procedures. It also reduces the risks associated with production accidents or equipment breakdowns. With the ability to master multiple tools and immerse users in real-world scenarios, VR simulations can reduce training time by up to 40% and increase retention rates by 75%, according to the National Training Laboratory.
3. VR Factory Floor Planning
In a virtual environment, manufacturers can walk around a 3D-modeled object. A 1:1 scale prototype reduces costs and time for a mock-up commission. This process allows for a more thorough evaluation of the design’s quality and ergonomic features, which cannot be achieved simply by viewing a 3D model on a computer screen. Within the virtual environment, logistics, security, and management can coordinate equipment location and test plant scenarios before it’s operational.
4. Maintenance and Repairs
Using VR technology for maintenance procedures can improve accuracy and reduce downtime by simulating complex repair scenarios and allowing technicians to practice in a virtual environment. This can help them to become more proficient and minimize errors during actual repairs.
5. Safety Training
With the help of VR technology, employees can simulate emergencies for training purposes. Such situations are often too dangerous or impossible to recreate in real life, leaving employees with only theoretical knowledge of how to respond to a crisis. Conducting safety tests and evacuation plans in an interactive VR environment can help employees acquire essential skills more quickly. A study published in the Journal of Manufacturing Systems reports that VR-based safety training led to a 25% reduction in workplace accidents.
Real Life Examples of Virtual Reality in Manufacturing
1. The Aerospace Industry: Boeing
Boeing adopted the use of virtual reality technology in designing and testing complex aircraft systems. Through VR, Boeing’s engineers can immerse themselves in a 1:1 scale model of their aircraft, allowing them to examine the design from the inside out, assess the integration of components, and simulate maintenance procedures.
2. Automotive Design and Assembly: Ford Motor Company
The Ford Motor Company has been leveraging VR technology in its vehicle design and assembly processes. Ford’s VR lab enables designers and engineers to work in a virtual environment to develop cars, trucks, and SUVs. The technology has allowed them to explore different design variations, assess ergonomics, and simulate assembly line workflows, which has significantly reduced development time and costs.
3. Pharmaceuticals: Pfizer
Pfizer has integrated virtual reality (VR) technology into its manufacturing processes, specifically for the design and configuration of its manufacturing facilities. By utilizing VR, they can virtually explore and navigate through a plant, visualize the placement of equipment, and optimize the layout to ensure maximum efficiency and adherence to health and safety standards.
4. Heavy Machinery: Caterpillar
Caterpillar Inc. utilizes virtual reality for two main purposes: product development and operator training. By creating virtual models of their heavy machinery, they can test and refine designs before moving to production, which results in the creation of high-quality products. Moreover, the company employs VR simulators for training their operators, who can gain experience in a safe and controlled virtual environment.
Trends Shaping the Future of Virtual Reality in Manufacturing
The manufacturing industry is about to witness an innovative transformation with the emergence of Virtual Reality technology. VR has become more affordable and user-friendly, making it accessible to all manufacturers, big or small, to leverage its capabilities in design, training, and beyond.
It is revolutionizing the quality control process by integrating with automated systems and creating virtual replicas for precise testing and monitoring. The synergy of VR with 5G and the Internet of Things (IoT) boosts its impact, delivering faster, more responsive experiences enriched with real-time data for accurate simulations and training. In summary, the future of VR app development services in manufacturing promises a collaborative, accessible, and technology-driven transformation, redefining the industry landscape.
Travancore Analytics offers top-notch VR specialists to help you choose the best VR equipment and technology stack for your project. We can also create a VR prototype and assemble a highly skilled team to complete the development cycle.
Contact us to learn how we can help you leverage VR technology for your manufacturing industry.