December 19th, 2023
Category: ar vr
No Comments
Posted by: Team TA
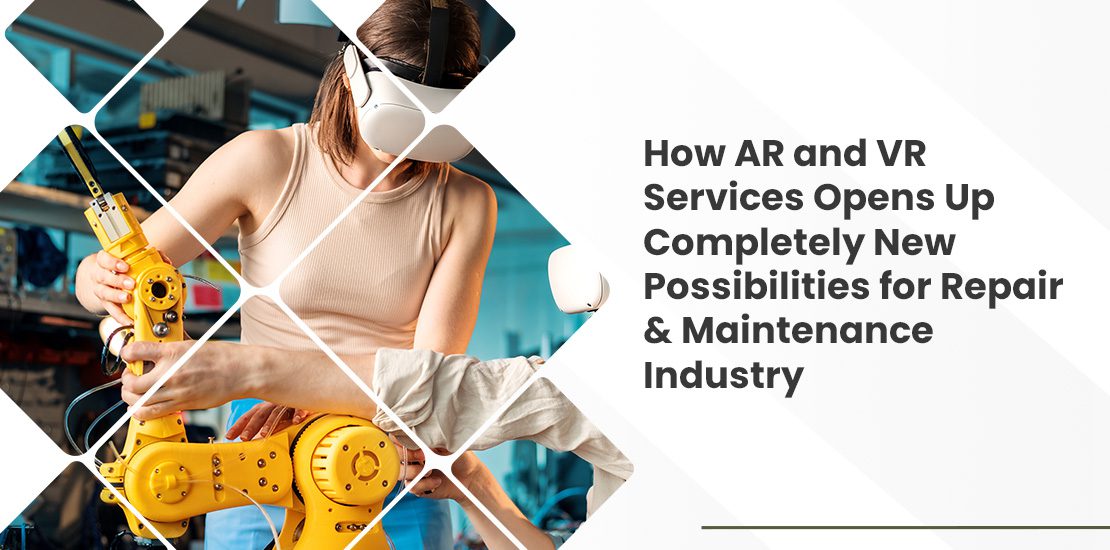
The fusion of Augmented Reality (AR) and Virtual Reality (VR) is paving the way for various industries in this era of technological advancements. Mark Zuckerberg, CEO of Meta Platforms, believes that AR and VR will become the next major computing platform after mobile. The repair and maintenance industry is one of the most promising areas that will benefit from these technologies. According to a Markets and Markets report, the global market for Augmented and Virtual Reality in repair and maintenance is expected to grow from $2.2 billion in 2020 to $5.7 billion by 2025, indicating the vast potential for industry-wide transformation.
Conventional approaches within the repair and maintenance industry rely heavily on physical presence, manual labor, and paper-based records, all contributing to inefficiencies. Equipment diagnostics and maintenance procedures are often based on guesswork or outdated manuals, leading to frequent breakdowns and extended downtime. Workers face various risks while working in hazardous environments, and the lack of real-time data and guidance puts them in further danger. According to a report by McKinsey & Company, inefficient maintenance practices can cause unplanned downtime, which can cost manufacturers up to $1 trillion annually. In this blog post, we explore how AR and VR are revolutionizing the repair and maintenance industry by streamlining operations, reducing costs, and improving overall safety.
Top 5 Applications of AR/VR in Repair & Maintenance Sector
1. Remote Assistance and Troubleshooting
With AR, experts can provide real-time guidance to on-site technicians or equipment operators, overlaying digital information onto the physical environment. This enables remote professionals to see what the technician on-site sees and share visual cues, diagrams, and step-by-step instructions, greatly reducing downtime and errors. It empowers technicians to efficiently diagnose issues and perform repairs, resulting in cost savings, improved efficiency, and enhanced safety, making AR an invaluable tool for remote support in this industry.
2. Interactive Maintenance Manuals and Instructions
Interactive maintenance manuals and instructions provide technicians with access to relevant information that is overlaid onto the equipment they are servicing. This includes schematics, operating procedures, and troubleshooting guides. This real-time guidance is hands-free and intuitive, making the repair process more efficient and error-free. The use of AR technology allows complex instructions to be visualized directly on the equipment, streamlining maintenance tasks, reducing human error, and accelerating the learning curve for new technicians.
3. Real-Time Data Visualization
Companies like Boeing and General Electric use AR to overlay critical data onto their equipment, empowering technicians with immediate access to performance metrics, historical records, and diagnostics. This data visualization aids in predictive maintenance, allowing issues to be detected and addressed before they lead to breakdowns. For instance, Boeing reported a 25% reduction in assembly errors using AR. This real-time data ensures optimal equipment health, reduces downtime, and significantly cuts operational costs, making AR an indispensable asset in modern maintenance practices.
4. Virtual Training and Skill Development
Technicians can simulate complex repair scenarios, gaining practical experience without real-world risks. This enhances their problem-solving skills, boosts confidence, and accelerates the learning curve. For example, companies like Siemens use VR to train technicians to maintain gas turbines. VR training is accessible, interactive, and particularly valuable for teaching safety protocols and hazardous equipment handling.
5. Simulation of Complex Repairs
VR simulations are a crucial tool for ensuring preparedness and proficiency in high-stakes repair scenarios. Technicians can immerse themselves in a virtual environment that replicates the equipment they need to repair. This hands-on experience allows them to practice intricate repair procedures without any real-world consequences. Companies like Lufthansa Technik use VR to simulate aircraft engine repairs. It’s a cost-effective way to improve skills, reduce errors, and enhance confidence when dealing with complex maintenance tasks.
Benefits of AR and VR in Repair and Maintenance
Improved Efficiency and Reduced Downtime
AR and VR services dramatically improve efficiency and reduce downtime in the repair and maintenance industry by providing real-time information and training. AR offers on-the-spot guidance and data overlays, enabling technicians to perform tasks accurately and swiftly. VR, on the other hand, enhances training, ensuring technicians are well-prepared to handle repairs. Both technologies cut the need for manual referencing, streamline processes, and minimize human errors. This efficiency results in faster troubleshooting and maintenance, ultimately decreasing equipment downtime, reducing operational costs, and ensuring optimal productivity.
Cost Savings through Remote Troubleshooting
Technicians can use AR to guide on-site personnel from a distance, reducing travel costs and downtime. In the aviation sector, companies like Airbus employ AR glasses to connect experts with technicians, saving significant travel expenses. Similarly, VR allows experts to diagnose and address issues without leaving their location. These technologies not only minimize travel-related expenditures but also enhance problem-solving speed and accuracy, leading to substantial cost savings for businesses in the repair and maintenance industry.
Enhanced Safety for Maintenance Workers
AR and VR technology services not only enhance safety but also contribute to a safer, more reliable work environment, decreasing accident-related costs. By providing real-time information and simulations, they reduce the risks associated with hands-on tasks. A study by the International Journal of Environmental Research and Public Health reported that AR-based training reduced workplace accidents by 12%, highlighting the potential for safety improvement. VR, through realistic simulations, allows workers to practice in a controlled environment, minimizing physical risks.
Reduced Skill Gap and Improved Training
AR and VR services allow trainees to practice complex procedures and troubleshoot equipment in a risk-free virtual environment. Workers can gain expertise at their own pace, without real-world consequences, resulting in a more skilled and confident workforce. This training approach not only reduces errors but also accelerates the onboarding of new technicians, ultimately increasing overall proficiency and knowledge retention in the repair and maintenance sector.
Final Thoughts
AR/VR development services are set to redefine the repair and maintenance industry as they integrate seamlessly with AI and IoT. The growing integration of Artificial Intelligence (AI), enabling intelligent equipment monitoring and predictive maintenance and IoT connectivity, with sensors providing real-time data will enhance the precision and speed of AR/VR applications. Moreover, spatial computing will enable more interactive and immersive experiences, allowing technicians to manipulate and visualize equipment in real-time. These advancements not only streamline repair and maintenance operations but also improve safety and efficiency.
In conclusion, AR and VR are not just emerging technologies; they are the catalysts for an extraordinary transformation in the repair and maintenance industry. From streamlining processes and enhancing worker safety to significantly reducing costs and bridging skill gaps, their potential is undeniable. Explore the potential of AR and VR to boost your business growth. It’s the perfect time to embrace digital technology for repair and maintenance. TA is a leading provider of AR/VR app development solutions with a proven track record. Partner with TA and take advantage of the latest advancements in technology to boost your business.